![]() |
Remake or Buy? Reconditioning Products at Xtra Power Energy Systems
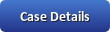
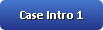
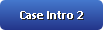

EXCERPTS
SUPPLY CHAIN RECONFIGURATION EFFECTS
REMAKE OR BUY?
Dutta was aware of the problems at the plant and called for immediate action. Together with Nanda, he worked out a detailed plan which involved the use of an adjoining facility on rent, installing the necessary equipment for the reconditioning process, and hiring additional manpower at a total cost of approximately Rs. 21.7 million (See Exhibit II for the breakup of costs). Sheikh, however, proposed that Xtra Power should outsource the reconditioning process to Revathi Batteries. Revathi’s core competency was in reconditioning used batteries and it had been in the business since 2001...
EXHIBITS
Exhibit I:The Battery Industry in India
Exhibit II:Detailed Break-Up of Costs